- The Challeges in Warehousing of Foodwear and Apparel Industry
- Improvements Brought by WMS System
In the context of the new economy and new retail, where fashion trends change rapidly, from the planning and production of front-end goods to the layout of warehouses and networks, and throughout various stages of the system, logistics and supply chain services require greater flexibility, digitization, and integration. Only an intelligent and highly adaptable warehouse management software system can assist supply chain warehouse operations in providing flexible services and meeting the diverse demands of the fashion industry, helping clothing companies reduce costs, improve efficiency, and increase their market share.
BEST SOFTWARE offers a full-scenario digital solution service. Among its rich product portfolio in China, QUICK WMS is a large-scale automated intelligent warehouse software. BEST Inc. has been deeply involved in the footwear and apparel industry for decades and has provided services to numerous renowned footwear and clothing brands through this software. Tested and refined through over a decade of supply chain practice, QUICK WMS can provide end-to-end, multi-channel warehousing solutions, supporting personalized requirements for B2B, B2C, multiple modes, multiple channels, and all scenarios. It can flexibly combine various standard services (received, dispatch, storage, returns, quality inspection) and industry value-added services to meet the high-quality warehousing service needs of the footwear and apparel industry.
The Challeges in Warehousing of Foodwear and Apparel Industry
Multiple Warehouses and Challenges in Shared Inventory Management:
As sales channels at the front end diversify, inventory has evolved from single-warehouse storage to multiple warehouses with graded inventory, spreading across multiple locations nationwide.
Significant Fluctuations in Seasonal Order Volumes:
Fashion trends change rapidly, and peak seasons demand high efficiency from systems and operations. Peak periods during promotions require high quality inspections and shelving.
Complex and Multiple of SKUs (Stock Keeping Units):
Footwear and apparel come in numerous styles, colors, and sizes, resulting in tens of thousands of SKU combinations, making it challenging to manage and categorize them effectively.
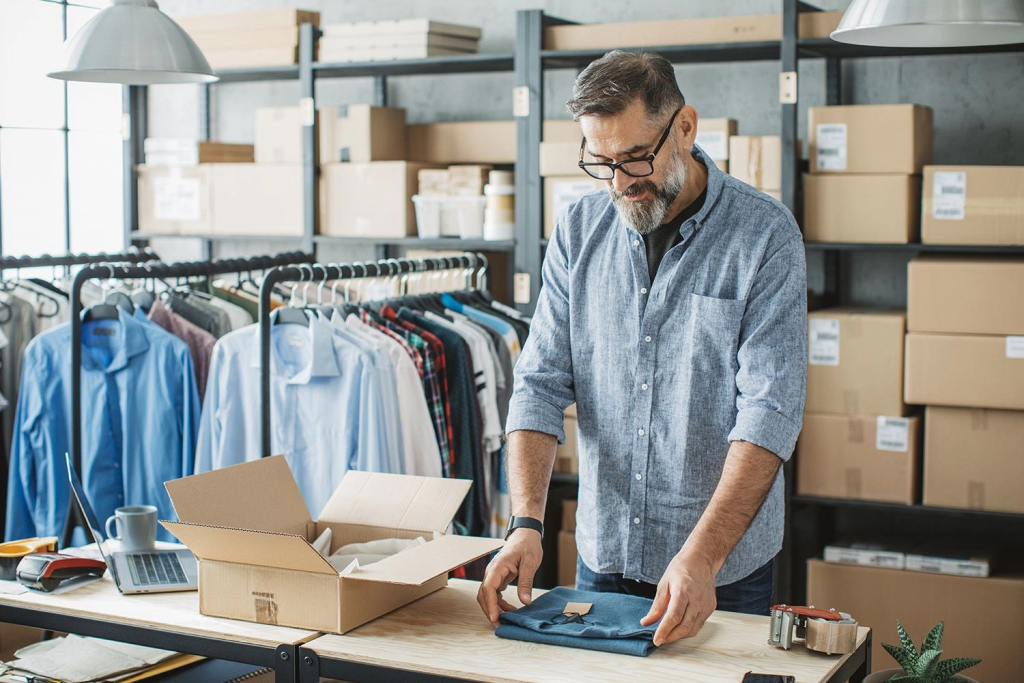
Improvements Brought by WMS System
Unified Inventory Management for Online and Offline Channels:
QUICK WMS system, through its supply chain middleware (inventory middleware and order fulfillment middleware), integrates orders from various channels such as public domain e-commerce, social e-commerce, live-streaming e-commerce, community group buying, as well as offline-owned stores, retail chains, distributors, and dealers. It supports integrated management of both B2B and B2C orders, multi-level collaborative warehouse management, and shared inventory.
Pre-Season Distribution, Mid-Season Replenishment, and Post-Season Returns:
Centered around the QUICK WMS system, a complete set of digital solutions helps customers establish a responsive supply chain system, covering pre-season product planning, distribution, mid-season replenishment, and post-season returns. This ensures a full-service response to store distribution, replenishment, transfers, and returns.
QUICK WMS's highly adaptable outbound processes and timeliness warning functions meet the delivery deadlines during major promotions. Intelligent inventory management strategies help warehouses quickly organize seasonal inventory changes, and quality inspection and returns functions facilitate speedy inspection and restocking for resale.
Inventory Management with Precision and Reasonable:
An experienced and professional implementation team offers customers services for warehouse area and location planning. Leveraging QUICK WMS's intelligent warehousing strategies for inbound stocking, warehouse replenishment, and inventory management, SKUs are distributed within the warehouse in a more rational manner in terms of location and quantity, facilitating efficient order picking.
Real-time and accurate recording of inventory changes with handheld devices throughout the warehouse ensures timely identification of inventory discrepancies. Convenient discrepancy handling functions promptly correct inventory discrepancies, ensuring that the accuracy of inventory, even for thousands of SKUs, can reach 99.99%.
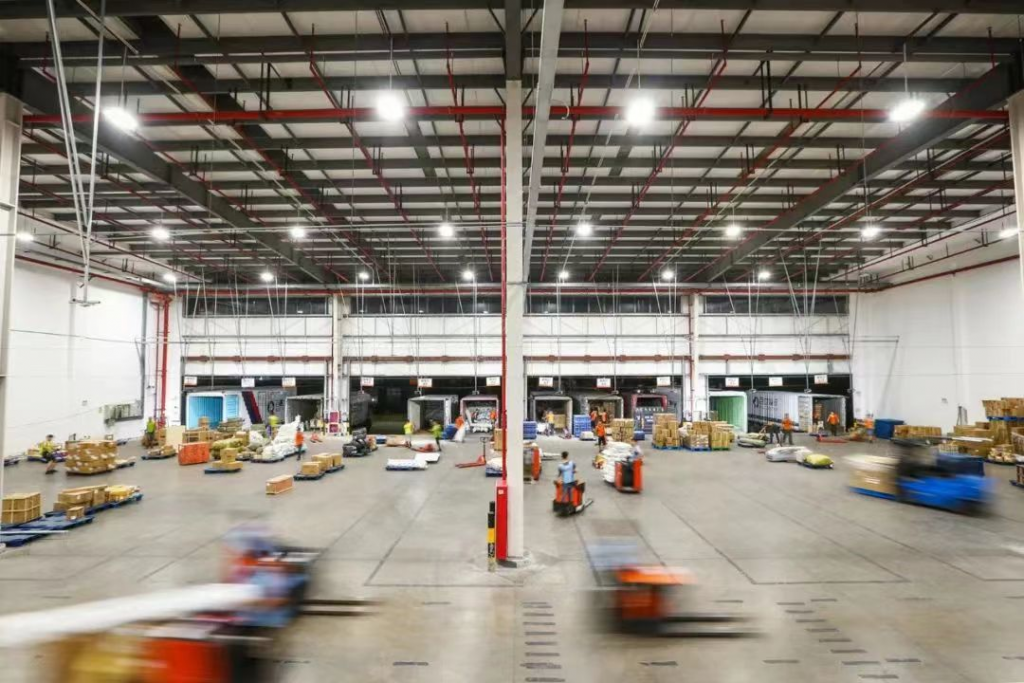
Curious to learn more?
To make an informed decision when selecting a Warehouse Management System (WMS), please call us for more inquiry & information. We will provide a free consultation to your warehouse business.